Heated Build Platform for Ultimaker
19 June 2012 at 7:30 am
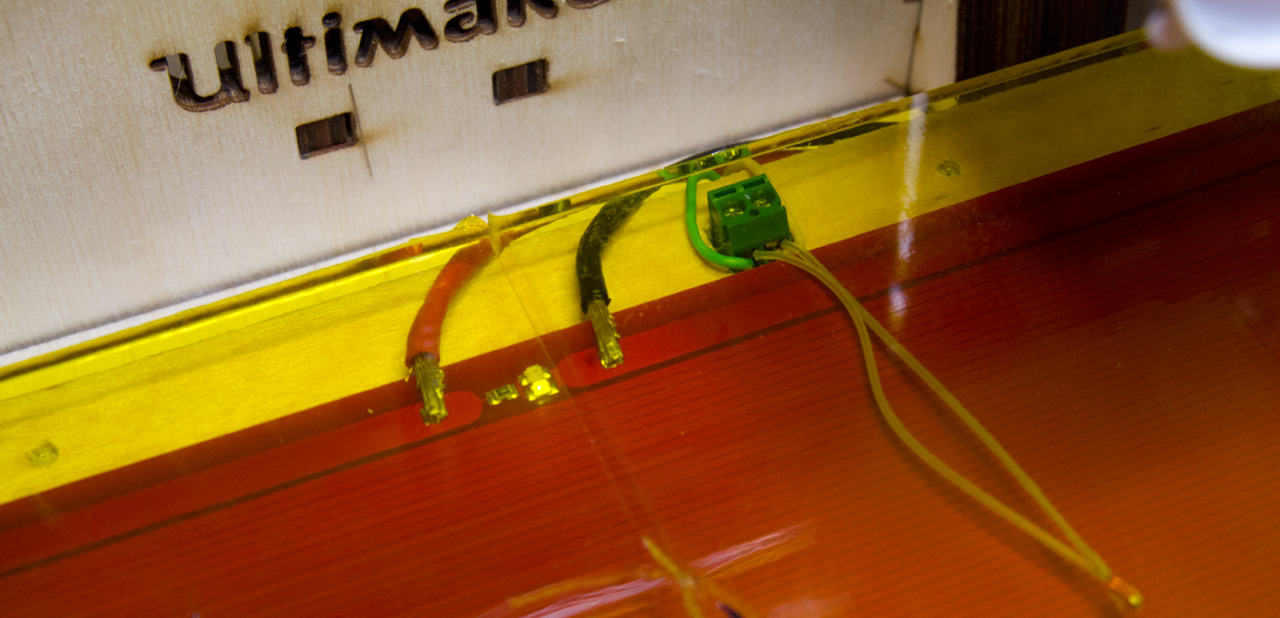
Note: updated description available here! While this is written for the Ultimaker, it should also work the same for any RepRap printers with similar RAMPS electronics.
One thing I disliked with using a Makerbot was it's dependance on printing with ABS plastic. ABS comes from fossil fules and is thus a limited resource. PLA usually comes from Corn and is thus fully renewable and to some degree also biodegradable. This was one of my main reasons to get a Ultimaker in the first place, but then it dawned on me that the 60 degree celcius melting point for PLA was going to be a problem for many of my projects. I had to make my Ultimaker capable of using both plastics: PLA for prototyping and ABS for lasting models.
Why
When you are printing with PLA, all you need is some blue painters tape to print on. ABS however, won't stick to that. In addition - ABS requires that you keep the model warm while printing and ideally it should be allowed to cool off slowly to avoid cracks due to the material shrinking. How warm the heated build surface should be will vary a little based on the plastic, but I found these tables in the Makerbot Wiki a good reference. 110-120 celcius seems to make the ABS that I use stick well.
You can also use a heated surface for PLA, but then you keep it at about 70 degrees celcius. A nice plus when printing PLA on a heated surface is that it requires virtually no force to remove the model once the surface has cooled. What I needed was a Heated Build Platform (or HBP for short).
What and Where
How does one make such a thing? The RepRap wiki has many suggestions but after reading through all the links, there was one design that really appealed to me. It's basically a PCB that barely has any components, but rather lots of copper. When power is applied to the PCB, the copper turns hot - just like in an electric oven or a hair dryer.
This PCB was designed by Josef Prusa and it's a perfect size for the Ultimaker (20 x 20cm). It also has a feature that I appreciate - it's made for 12 volt operation so no need to mess with AC electricity that could kill you! There are many similar methods used in various industries today and if I didn't want to use 230v, I'd probably get the SRFG-808 from this site (GBP 44).
Josef's design is called MK1 but the wiki also contains an alternate version here is a derivative version with a hole in the center. This one is called MK2. These both work the same, but there's really no need for the hole in the middle. This description should work for both though. After reading some warnings and sad stories from people that bought "cheap" PCB copies on Ebay, I decided to get a MK1 from a reputable supplier that would also give a little back to the creator of the PCB. I didn't find any good tutorial on how to set the heated bed up, so I figured that I'd write how I did it for others to find.
The nice thing about shopping from companies like Ultimachine is that they know what else you need. I also picked up a 100k Thermistor with PTFE sleeving from them to measure the temperature. I also picked up some 100mm Kapton tape for covering the print surface. You can also use thermistors with 10 or 200k resistance or a thermocouple based on AD595. Thanks to Daid's great Marlin Builder, you can adjust your Ultimakers firmware to reflect the correct hardware. Speaking of Daid - if you're not using his Cura software for your Ultimaker - you're missing out Big Time. To me it's been the difference between a good purchase and a bad one!
The Power Supply that comes with the Ultimaker cannot drive both the machine and a heated bed. Due to this, most others have gone the path of adding an additional power supply. Some have even replaced the existing one, but due to the limited space beneath the Ultimaker I had a hard time finding one that could both fit inside as well as provide a decent airflow to keep things cool. What I ended up getting was an external power brick that could deliver 12.5Amps of 12 volt. The PCB only pulls 10A maximum so I figured that would be sufficient. Having two power bricks isn't "sexy", but it does not require any big changes to the Ultimaker's stylish wooden body and it does not add more noise. Also - they had one at my local computer supply store, so I could just pick it up. It's a little pricey at GBP100 / $150 but I still like the solution.
So I had the heating element, a way to power it and a way to measure the temperature. Now I just needed a way to turn it on and off when required. I was thinking of building my own solution, separate from the Ultimaker. The Streacom PSU had both 5v and 3.3v so I could easily add an Arduino Mini to control the heated bed. I would need a screen or at least one 7-segmentd display, some buttons for control and with this I could even pimp my Ultimaker by letting this control some RGB LEDs. Yeah. That's what I'll do! I ordered a bunch of components from Adafruit and Sparkfun, but as I waited for these it started to annoy me that I couldn't combine this with the Ulticontroller.
I started digging and it turns out the Ultimaker PCB had lots of what was needed. There's a connection for the thermocouple and a PWM output with a solid MOSFET… I wonder if that couldn't drive a standard relay for a car? I picked up a 30 amp relay at my local car supplies and it worked like a charm with the 19 volt output of the Ultimaker. I got great help from this Instructable measuring the Relay. The relay cost $6.50 and I also got a nice socket for $4 that I could use for simple mounting and replacement (if required).
This is how the end result looks and below is a tutorial on how to do this yourself.
Bill of Materials
Here's the list of components I've used:
- MK1 PCB. See RepRap wiki for suppliers. ($50 from Ultimachine)
- 100k Thermistor ($2.75 from Ultimachine)
-
Streacom 150 watt external PSU ($150 at my local PC store) - 360 watt industrial type PSU from Ebay ($50 with shipping)
- Relay + relay socket with cables. Make sure it's a 5-pin one, so it's both open/closed. ($10.50)
- ATX 24 to 20 pin conversion cable ($8 at a local computer store)
- 25 x 25cm plywood piece, 10-12mm thick, as flat as possible ($2 at a woodshop)
- 24 x 24 cm sheet of 4 mm glass with 4 holes spaced 209mm apart ($30 at my local glass-shop)
- A 4.7k resistor
- A few 3mm o-rings (rubber gaskets) that fit the holes in the glass sheet
- Four 4-6cm, 3mm bolts
- Some 3mm nyloc nuts, washers and other spare parts that came with your ultimaker
- Kapton tape
Tools
- multimeter
- basic soldering kit
- Drill
- Having an Ulticontroller is a huge plus for reading the temperature
Alltogether, the cost for my heated bed was about $150. I also could have saved a little by not getting holes made in the glass but rather use bulldog clips like Josef Prusa did. That would have saved a few dollars as well, so the total cost could have been as low as $100. Also note - these prices are from Norway ( = everything is expensive) so your bill will probably be lower than mine.
How
So - how to put this together then? It's not hard at all and I've also made some custom 3D parts to make it easy to mount the hardware.
1. Print the adjustment screw pieces
Printing these before removing the old build platform will save your fingers later on!
2. Drill 8 holes in the plywood square
Make 4 holes (3mm) that match the position of the adjustment screws of the original build platform. Then make 4 holes that match the position of the holes in the PCB. Make sure you drill all these very precisely or it won't fit.
3. Remove the old platform
Remove the acrylic and unscrew the screws. Save the screws as you'll use these later.
4. Mount the new adjustment screws
Take one long screw, one nyloc hex nut and one plastic screw-handle (eye-shaped) and put these together. These provide a solid adjustment screw for the bed and the screw-handle makes them much easier and precise to use than the hex-wrench. Once all four are put together, screw them into the delrin holes - but this time screw them in from the bottom. Using an electric screwdriver/drill is recommended. Tiresome!
5. Mount the PCB on the Plywood
For this, you can use the old "adjustment" screws. I put a hex-nut between the Heater PCB and wood, and another hex above to keep things in place. On top of this, I added a washer. In the picture below I've also added the springs from the old setup. Don't do this. It was just an experiment. O-rings are smarter.
6. Mount the Thermistor
It is nice to have a way to measure the temperature before you hook the Heater PCB to it's power. There are two things to do here. First you need to solder a 4.7k resistor on the Ultimaker's PCB. Unscrew the Controller PCB and take it out of the machine. The resistor should be added where it says R4 on the Controller PCB.
Next, make two wires that are about 70 cm long. These should be of the standard, thin type used in the rest of the machine. Guide the cables down through the rear, right cable duct. Connect these to the outer two pins on the connector marked "Temp 3" (as shown in this picture). Next, put the fan-thingie back on the Ultimaker Controller PCB. If you forget this, you'll easily destroy it.
Connect the other end of the wires to the Thermistor. I used a 2-pin terminal block as the thermistor can be hard to solder due to it's ability to withstand high temperatures. Now it's time to turn on the Ultimaker and test it! To do this, you'll need a custom firmware version. I assume you already use Cura for slicing and printing your models? Then you already know that Daid makes some great software! Making the custom firmware is really easy with his Marlin Builder script. Be careful to not adjust anything you don't know what is… Under "Heated bed temperature sensor", select the sensor you got. There are several 100k thermistors in the list, but if your isn't listed (or even marked in any way) just go with the "100k thermistor" option. If you have the Ulticontroller, check that one off the list as well and click the "Build Marlin" button.
At the top of the page there will now be a download link for a ZIP with the windows install file (that I used), as well as the .HEX file itself. Once the firmware is updated, it's time to test! If you have the Ulticontroller, you should now see another temperature reading and if you touch the temperature sensor, the display should change to reflect that you are (hopefully!) warmer than your surroundings. If you want to test it at higher temperatures, stick the thermistor to the printers extruder-head and set a new temperature with the Ulticontroller.
PS: Don't worry about the heat damaging the thermistor. It should be rated for more than 300 degrees and you should not go above 240 to avoid blocking your print head with burnt filament… Just test that the temp is fairly correct up to 110-120 as that's the highest you'll need to go.
7. Mount the relay
Solder a couple of wires (about 80 cm) to the heater PCB. According to this chart, these cables should be no less than 1.3mm thick to carry 10 amps safely. I used 2mm to be on the safe side, but that's probably not required. Guide the cables down through the rear, right cable duct as you did for the thermistor. Don't pull all the cable to the bottom as you'll want to be able to move the Build platform up and down without pulling the wires.
Next up is the Relay. I used an automotive relay since I know that they are made to withstand a lot of power and they are dirt cheap. Any relay rated above 10A(mperes) should be fine as long as the voltage is more or less the same as the 19v the Ultimaker will output. Autos use 12v and are rated for 30A so that should work for most relays.
Measure the relay according to these instructions and make a note of what color the different cables are and what they should do. If you got a relay like the one I got (5 cables), there will be_
- Two cables where you apply power to close the relay (connected to the Ultimakers output)
- The two cables that will be connected when the relay is closed (external power goes through here)
- One unused cable
In the linked tutorial, the first two are referred to as COM and NO. On the relay that I was using, these are referred to as 86 and 85:
Between these, you should be able to measure a connection but the resistance should not be very high. Connect these to the Heated Bed output, close to your Ultimakers power jack.
On my relay (see below) the pin marked 30 is common and pin 87a is the normal position. When I measured these and found a fairly high resistance (as indicated in the tutorial). That meant pin 30 amd 87 should connect when the relay became energized. So by simply connecting one of the cables for the heated bed through pin 30 and 87, the Ultimaker would toggle power on/off as required.
8. Prepare the ATX connector
It's not much that you need to do with the power supply itself, but you'll need to tweak the ATX conversion cable a little. Start by cutting off the 24-pin side of it and then remove the wires you don't need. Since the PSU has some amperes to spare and it's easy to keep the 3.3 and 5v cables, I saved some of these in case I want to add an Arduino for some custom lighting or something. According to what I've read, the pins in the ATX connector are rated for 6A each, so to safely use 10A I connected two grounds and two 12 volt together.
Yellow = 12v, red = 5v, orange = 3.3v, black = ground (ref)
9. Testing time
Make sure you re-attach the fan over the Controller PCB and then flip the Ultimaker over to normal position. Now you can test if you connected it correctly by setting the heated bed temperature to something above room temperature.
If you are using the Ulticontroller, just select the Heated bed from the menu. If you don't have the Ulticontroller, you will need something that can connect to the printer and send it commands. Both Printrun and ReplicatorG can do this. In Printrun, there's a separate window for entering commands directly. In ReplicatorG, you just make a new file, type the command into the gcode-tab and then send it to the printer as you would when printing. The command to send is:
M140 S70.0
This should set the temperture of the bed to something near 70 degrees. When the Ultimaker reads the Thermistor to be too cold, it will apply power to the Heated Bed output and close the relay. When the relay closed, I could measure a decent resistance from pin 30 to 87, but no longer from 30 to 87a. The connection was confirmed! My next step was connecting it all to the Heatbed PCB, place the thermistor on the Heated bed and test the complete setup.
Note: Since 1.5.4 of the electronics, the Ultimaker has a 55A MOSFET on the heater connection. This should be sufficient to switch the power to the bed directly, but I don't know enough about electronics to confirm this. Using a relay is within my scope of knowledge, it's totally clean and also separates the two completely in the case of an error. It would be great if someone wiser than me could comment if direct switching is now possible!
I tested thoroughly and measured with an IR thermometer what components became hot as the bed heated. On the tiny PCB that distributes and converts power became hot after 3 hours continous heating. It's the square, black component that becomes warm - about 70 degrees. I made a mounting bracket for attaching it to the bottom of the Ultimaker and on this one, I added screw-holes for a 20mm PC fan. These can be bought in any computer supply store. They operate at 12 volt and it keeps the ATX connector at room temperature even when the bed is constantly on for 10 hours or more.
10. Mount it all on the Ultimaker
Once you are sure the electronics work as intended, you can wrap up the build. First, secure the electronics in place beneath the Ultimaker. For this purpose I've made some more printed parts. Make sure that the holder for the ATX-plug-holder is printed in ABS and not PLA (so it handles heat better). You just slide this one onto the connector and screw in place a 20mm fan. Connect the fan directly to the 12v lines on the connector, drill the one missing 3mm hole under the Ultimaker and fasten the holder with some of the 3x10mm spare screws that came with the machine as well as some nylock nuts.
Next, mount the power jack. This requires some drilling to get perfect, but I'm quite happy with the result.
When this is in place and the cables have been adjusted a little, it doesn't look too messy beneath:
You can see the connections more clearly in this image (click for full rez):
I mounted the 4.7k resistor on some header pins to see if I could get more precise temperture readings by tweaking the resistor values. In the end, I ended up going with the 4.7k anyway so I should probably remove the headers and solder it permanently.
Put the plywood/pcb on to the adjustment screws. Cover the glass plate with kapton tape and put it onto the PCB. Adjust the height of the Heater PCB screws, so the top is flush with the glass surface. Add o-rings (rubber gaskets?) between the 3mm screw and the glass. This ensures that the glass lies steady, but still can expand a bit as it gets hot.
Next we need to make sure the bed is entirely level. The standard rule about being able to pull a sheet of paper between the print head and the surface applies. Move the print head around the entire surface to make sure it does not touch the glass/kapton surface.
Adjust the length of the wires for the Heater PCB and the Thermistor. Make sure to leave some centimeters of wire so that the platform can move all the way up/down without pulling the cables.
That's it. Set the temperature of the bed depending on your plastic type and print away!
The result
The Heated Bed works just as intended and I'm very happy to have it all working. Before doing this, I thought that the constant clicking of the relay would drive me crazy bt it's really no problem. The printer itself is so loud that it's merely a drop in the ocean. The setup has been working non-stop for almost two weeks now. For PLA printing, it's simply fantastic. Models stick like glue when the platform is at 70 degrees, but come loose very easily when the platform cools off.
For ABS, it works but it's not perfect. It takes about 10 minutes to get up to 100 degrees. This is decent, but quite a long time. To get to 110, it's even longer and I can just barely go beyond that. The thing is that I need the bed to go to 110 and maybe also 120 for the ABS to stick properly. Now, it works fine for models that have a large area of contact, but smaller models often come loose since the plastic isn't sticking well enough. Due to this I'm now experimenting with closing the gap around the build surface using high-temperature silicone. This looks good so far, but I'll update here once I get to test a little more.
Update June 23rd 2012:
Closing the gap around the Heater PCB gave no measurable effect! Have to say I'm a bit stunned by that one. It takes just as long to get up to temperature and it's just as hard to go higher. I guess that means that my Power Supply is too weak. I'll test this with a computer PSU and update here later.
Update July 25th 2012:
Tried with a 450 watt PSU (12V/16A) and found no noticable difference. Could it be that I need to bundle the two 12V lines? Thinking aloud: 12V * 16A = 192 watts. Multiplying this with two seems like an idea, but I'll need to find documentation on how this PSU (KDM-1UFX425) is built then. I don't want to start a fire...
Update 3 August 2012:
Turns out that my idea of maintaining some distance between the glass and the PSU wasn't such a good idea after all. When testing with a different PSU today, the glass cracked since the glass was bigger than the PCB and thus wasn't heated equally. I have a spare 20 x 20 cm glass that I'll fix to the PCB with bulldog clips like all others do. I have those already.
Update 5 August 2012:
Turns out I simply did not have enough power. Instead of using the 120 watt Streacom PSU, i will be using a 360 watt industrial type PSU (12V / 30A) that I got from Ebay for about $40 (plus shipping). You can see this PSU in the image below. The drawback of this one is that I sort of have to deal with 220 volt, but it's quite well protected so it's not scary in any way. I will also have to print some feet for the Ultimaker before mounting this permanently as it's a little too tall (5cm), but it'll fit nicely just behind the front of the machine. This PSU also has the extra power to drive LED's and such so I can now "pimp" my Ultimaker a little more 😉